In the ever-changing world of manufacturing, tech advancements are constantly reshaping what we can achieve.
Staying updated with the latest metallic news and insights on Metalswire is crucial, along with keeping an eye on emerging trends. One standout innovation is 3D printing, which is shaking things up in the steel and metal industries. This blog dives into the fascinating realm of metal 3D printing, exploring how it works, its benefits, and the significant impact it’s set to have on the industry.
Exploring metal 3d printing
Metal 3D printing uses additive manufacturing (AM) techniques to build complex metal parts layer by layer. Here’s a quick rundown of the process.
Creating the digital design
It all starts with designing a 3D model using Computer-Aided Design (CAD) software. This model acts as the blueprint, detailing dimensions, geometry, and other specifications.
Slicing the model
Next, the digital model is sliced into thin horizontal layers, each representing a cross-section of the final product. Slicing is crucial for turning the 3D model into printable layers that the 3D printer can handle.
Printing the component
Techniques like Direct Metal Laser Sintering (DMLS), Selective Laser Melting (SLM), and Electron Beam Melting (EBM) come into play. DMLS and SLM use a high-powered laser to selectively melt metal powder, building it layer by layer based on the sliced design. EBM uses an electron beam in a vacuum to melt the metal powder, offering unique material properties and process control.
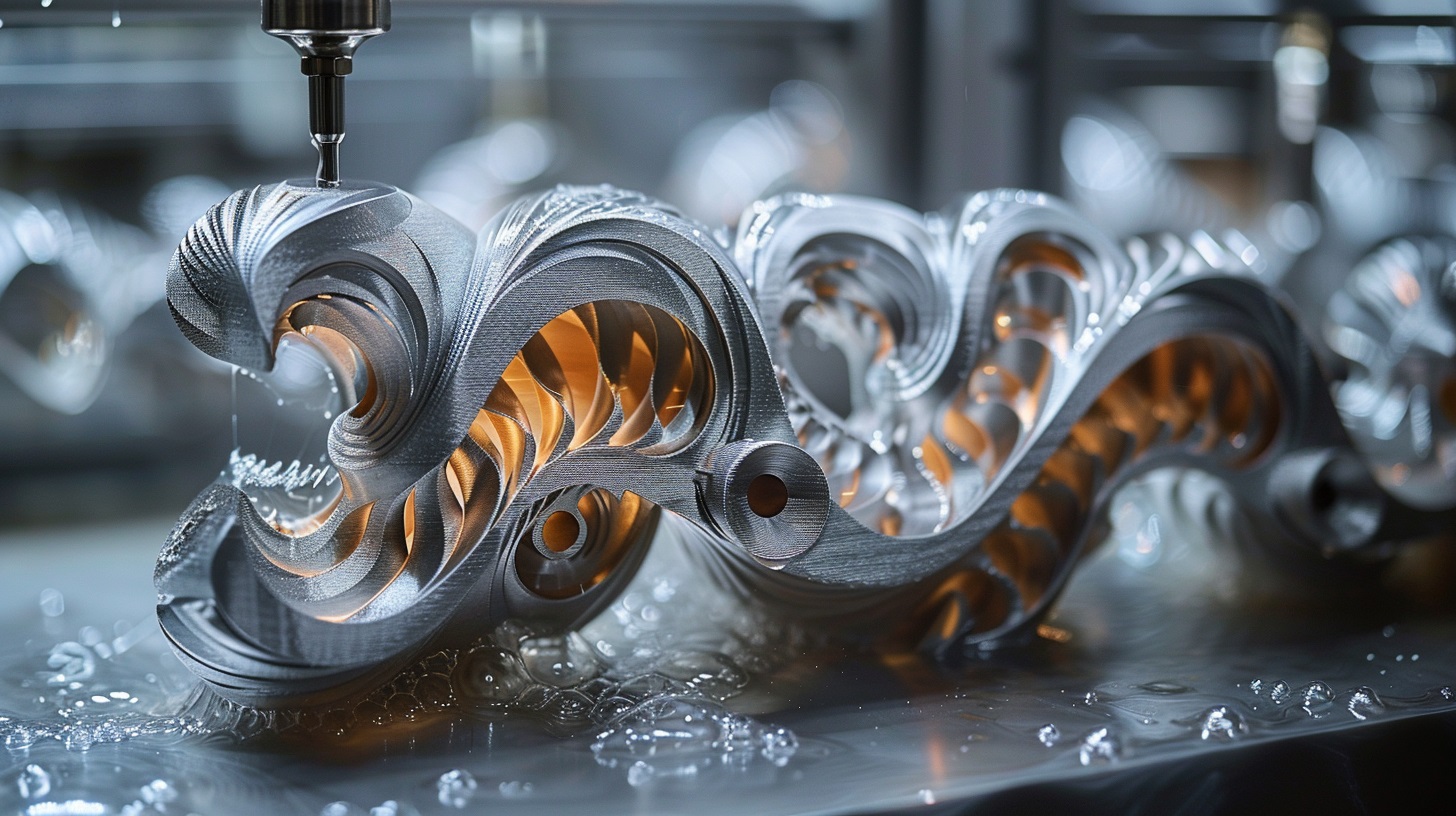
Adding support structures
Depending on the part’s complexity and the printing technique, support structures might be needed to keep overhanging features from deforming or collapsing. These supports, usually made from the same material, are removed after printing.
Post-processing
After printing, steps like heat treatment, machining, and surface finishing may be necessary to get the desired mechanical properties and surface quality. Heat treatments like annealing or stress relieving can boost material strength and stability, while machining might be needed to achieve precise tolerances or specific surface features.
Key advantages of metal 3d printing
Metal 3D printing is revolutionizing the manufacturing landscape by offering unparalleled design flexibility, sustainability, and efficiency. By transcending the limitations of traditional methods, this cutting-edge technology allows for the creation of intricate geometries, reduces material waste, and supports rapid prototyping.
It empowers manufacturers to consolidate complex parts, achieve lightweight designs, and embrace on-demand production with customization capabilities. Let’s explore how metal 3D printing is reshaping the future of manufacturing.
Design freedom and complexity
Metal 3D printing frees engineers from the limitations of traditional manufacturing. It easily produces complex geometries and organic shapes that were once difficult or impossible to create. This freedom allows designers to optimize parts for performance, functionality, and aesthetics.
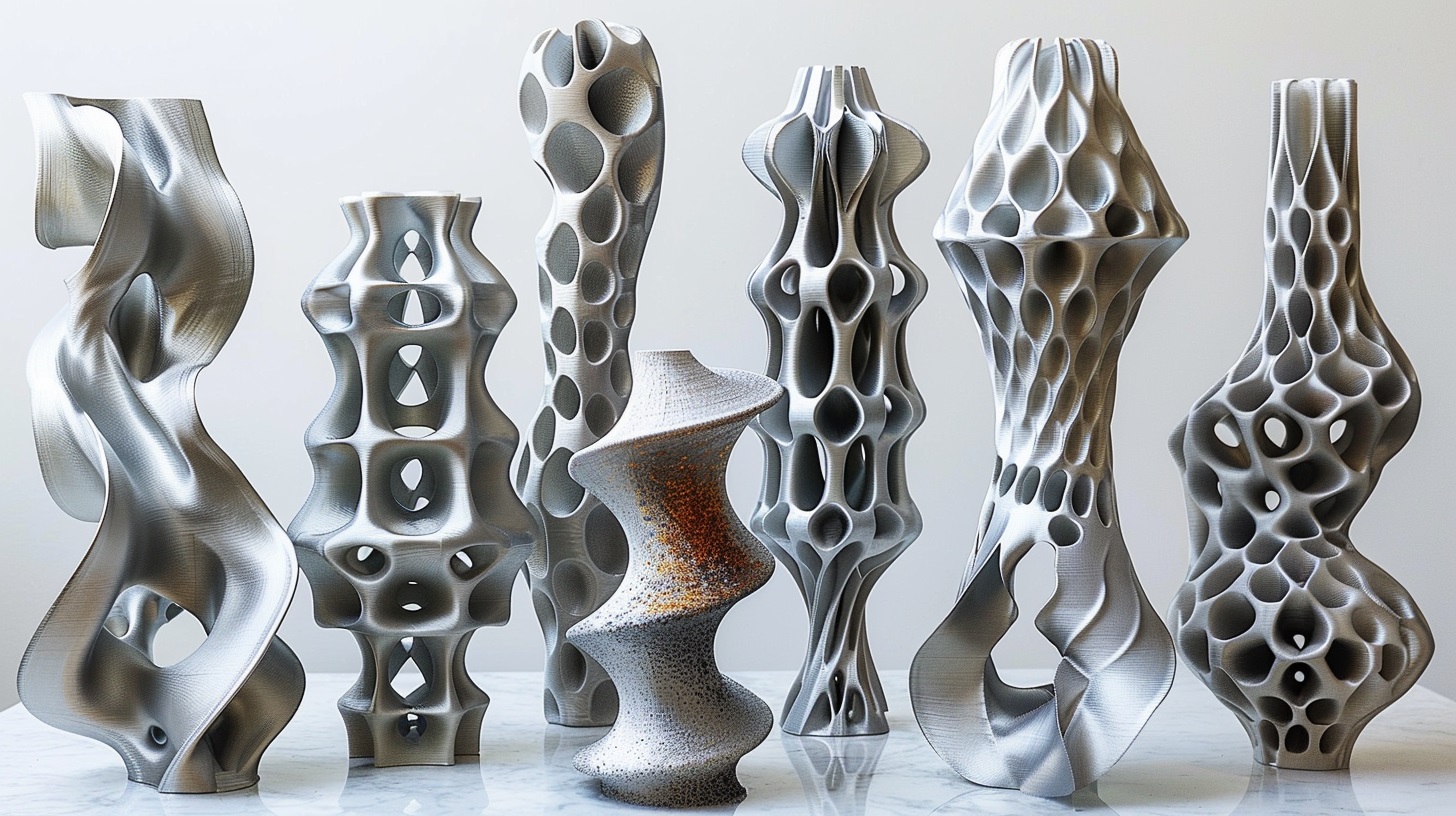
Reduced material waste and resource optimization
Traditional manufacturing often entails substantial material waste due to machining parts from solid metal blocks. In contrast, metal 3D printing adopts a “just-in-time” approach, using only the necessary metal powder for each component. This minimizes waste and optimizes resource usage, making the process more sustainable.
Rapid prototyping and iteration
In today’s competitive market, speed is crucial. Metal 3D printing supports rapid prototyping, enabling quick and efficient design iterations. This accelerates the product development cycle, reduces time-to-market, and helps companies stay ahead and swiftly adapt to changing customer demands.
Complex part consolidation and lightweighting
Metal 3D printing allows for the integration of multiple components into a single part. By removing the need for assembly and reducing joints, manufacturers can enhance structural integrity, decrease weight, and boost performance. This simplifies assembly, reduces costs, and optimizes end products.
On-demand manufacturing and customization
The flexible, on-demand nature of 3D printing supports just-in-time production. Manufacturers can produce components as needed, minimizing inventory storage and the risk of obsolescence. Additionally, customization becomes cost-effective, enabling tailored solutions for specific customer needs.